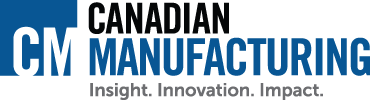
Pump maintenance key to uptime at Redpath Sugar refinery
by Rebecca Reid
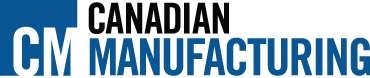
Standardized equipment and monitoring make up award-winning pump improvement plan
Toronto—The iconic Redpath Sugar plant on Toronto’s waterfront has an ongoing pump improvement program credited with boosting manufacturing uptime.
The plant was recognized with an award during Pump Appreciation Day in 2012; a global event held by ITT Goulds Pumps, based in Seneca Falls, NY.
With the 2013 awards less than a month away, Frank MacLachlan, maintenance manager at Redpath Sugar Ltd., reflects on the role pumps continue to play in the manufacturer’s longevity.
The company has been crafting sugar on Toronto’s Queens Quay since 1958, though its roots go back to 1854. The site is home to two buildings, a production facility and the Redpath Sugar Museum.
The plant underwent a $40-million modernization and expansion in 1997, but some legacy equipment and components remained. In the early 2000s, managers decided to launch a pump renewal program.
“There was a certain degree of obsolescence we wanted to address,” MacLachlan says. Parts for older pumps were becoming harder to find—and more expensive. Plus, Redpath wanted to standardize pumps across the board and get rid of its redundant back-up system.
Pump equipment is vital to Redpath’s operations as the sugar goes through several stages in a liquid state before being turned into crystals.
The first challenge was finding the right supplier. Redpath ultimately went with Mississauga, Ont.-based Rudi Kovacko & Associates, a distributor of multiple brands.
“We wanted a local service-person who could provide personal service for everything, from engineering questions to maintenance, and for consulting in different pumping applications,” MacLachlan recalls.
The company’s diagnostic services were also appealing, he adds. Kovacko takes in pumps that have failed and tries to figure out the root cause.
Redpath settled on two different models—a low-flow ANSI process pump, and a slurry pump.
With standardization in the bag, Redpath moved ahead with plans to get rid of the back-up pumps; opting to go with preventative and condition-based maintenance instead.
“Think of it like a spare tire on your car. We’re driving without a spare because we’ve standardized in a manner that allows us to run without one,” he explains.
Predictive maintenance technologies allow Redpath to troubleshoot to avoid failure. Tools include:
• Vibration technology
• Thermography
• Oil analysis
• Ultrasound
• Eddy current analysis
Shedding the back-up pumps have cut costs, but the over-arching goal is narrowing the time between pump failures, MacLachlan adds.
To that note, variable frequency drives installed on some of the pumps’ motors are improving production and reducing failure rates.
MacLachlan has also noticed energy savings, and benefits related to shedding a number of control valves that were using compressed air. The valves were also taxing maintenance labour, especially in instrumentation.
Uptime has increased year-after-year since the drives were installed, he notes.
The next phase of the continuous improvement plan is standardizing and replacing mechanical seals.
Redpath has selected AESSEAL and so far, has standardized on the vendor’s CSSN model, due to its double design.
The key takeaway though, is the pump improvement program doesn’t have an end date. As technologies and maintenance strategies continue to improve, Redpath will move in lock-step to keep the sugar—and revenues—flowing smoothly.
Related Industry gears up for 2013 Pump Appreciation Day in April