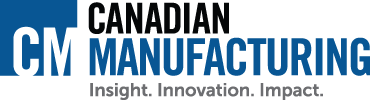
Additive manufacturing gaining ground through reputation
by Dan Ilika
3-D printing process cost-effective alternative to traditional machining
In an industry hungry for innovation—yet never short of skepticism—it often takes time for new technology to catch on.
Now, after close to 30 years, additive manufacturing is turning skeptics into believers as the technology begins to gain a reputation as a viable alternative to traditional machining.
Using three-dimensional images, the process transforms design files into objects layer-by-layer using powders made from glass, sand or metal.
It leaves little to no waste, a big sell in today’s cash-strapped manufacturing environments.
Also known as 3-D printing, the technology was showcased at the International Manufacturing Technology Show (IMTS) in September in the Emerging Technology Center, recognition not only of how far it has come in its three decades of use in manufacturing, but of how far it has left to go in it quest for legitimacy.
“There are a lot of changes (in the technology), including a major one which is public acceptance of the process of additive manufacturing,” says Nick Studley, sales manager with ExOne, a Pennsylvania-based firm specializing in additive manufacturing.
Studley says ExOne has been working in additive manufacturing for approximately 15 years, and a lot has changed in that short period of time.
Additive manufacturing started out in plastics, and over the last 10 years the cost of that equipment has come down and its reputation has grown, making way for the use of sand and metal.
“With everybody’s familiarity with the plastics machines it’s no shock that we’re now doing sand and metal,” Studley says.
Where the technology has made its biggest strides is in casting and mold-making, with the introduction of sand drawing interest from the automotive industry.
“Typically to get the molds and cores you need wooden patterns,” Studley says. “We remove the need for the wooden pattern, (which) significantly shortens the cycle to get your casting by three to five weeks.
“Instead of storing the wooden patterns in a warehouse you can put (them) on a memory stick.”
Additive manufacturing for prototype parts and low-volume production is extremely cost-effective, though Studley says at present production numbers need to stay low in order to maintain that edge over traditional machining, which is based on removing material to form a part.
“If you need 150 of something, the odds are it will probably be more effective to go ahead and do the conventional pattern from a cost-per-part standpoint,” he says.
One of the biggest upsides for additive manufacturing using plastics or metals is the waste reduction, which is a fraction of the cost incurred through traditional machining.
“I think that’s true of almost any additive manufacturing process,” Studley says of the drastic material waste reduction. “In our case (on) the metals side there is a little bit of scrap generated from our stilting requirement (pieces removed after infiltration for increased part density), but beyond that we’re not making any (metal) chips.”
Using metal powder, the process machines parts as large as 15x15x29.5 inches.
This is attractive to many stalwart industries, with mining and downhole drilling as the largest metal industry segment using the process.
Additive manufacturing may never supplant traditional machining, but 30 years from its inception the technology is reputable enough to help transform an industry.