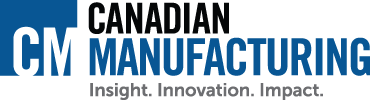
6 needed strategies in your manufacturing Process Safety Management program
by Emily Newton, Editor-in-Chief, Revolutionized
Some work environments require more risk considerations than others, but nobody needs to settle for an unsafe workplace.
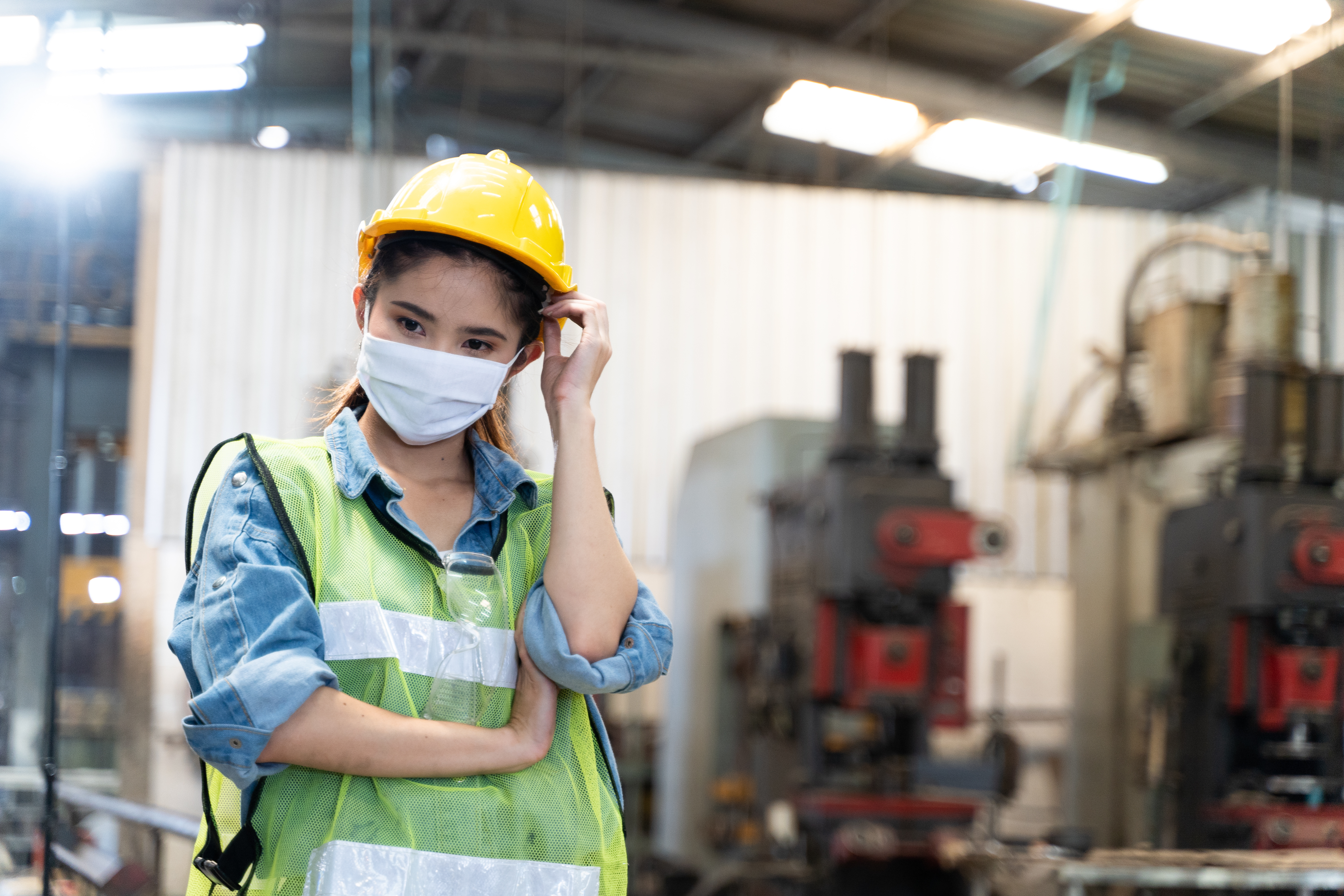
OH&S professionals can convert COVID-19 chaos into an opportunity to build a robust system. (Adobe Stock)
Process safety management is, itself, a process. The Occupational Safety and Health Administration (OSHA) continually updates its guidance regarding safety programs, often in response to headline-worthy workplace incidents.
Companies should not wait for the worst to happen. Employers can keep their PSM programs up to date to stay ahead of changes made by regulators. Here are several strategies to create, maintain and update a modern PSM program.
1. Employee Buy-In
Employees must have emotional and organizational buy-in. PSM programs should always include input from the workers facing risks in the workplace, and any time changes to the PSM are discussed, employee representatives should be present to add their perspectives.
2. Analysis of All Hazards
OSHA’s mandates regarding PSM standards require employers to analyze all hazards employees face. Leaders in the maintenance and engineering departments should conduct these investigations in a team format.
Each team should have at least one individual who takes thought leadership over the hazard-avoidance methods deployed in their department who clearly communicates safety material with the rest of the workforce.
3. A Process for Cleanups
Industries can be diverse yet still face common risks. Spills and accidental releases of chemicals, vapours and contaminants are all-too-common examples. Therefore it’s important to have the materials on hand to manage spills effectively. Spill kits can be universal or tailored to a specific industry, so it’s important to make sure you kit complies with OSHA and EPA regulations.
OSHA requires employers to have an emergency preparedness plan in writing. It should include potential workplace risks, including hazardous waste, chemical storage, and procedures for interacting with cleaning or environmental equipment, as applicable.
4. Pre-Startup Inspections
No process safety management program is complete without recognizing the potential threat posed by powered industrial equipment. This includes conveyors, lift trucks, forklifts and any other heavy implement that must work in concert with human bodies. OSHA requires operators to inspect these assets before startup.
Additionally, any powered equipment being returned to service after a period of disuse requires an additional inspection, regardless of previous results.
5. Compliance Inspections and Audits
As part of their process safety management plans, employers must conduct regular compliance audits and retain two or more of their most recent reports.
Inspections and audits are important for proving companies have taken all reasonable precautions and that employees are following guidelines. Employers should examine positive reinforcement for compliant behaviours versus negative reinforcement for noncompliant ones. The use of either or both should be outlined in employee handbooks and PSM documentation.
6. Expectations for Managing Change
Change management is one area where lapses in communication abound, and it must be addressed in PSM documentation. Failing to fully understand and communicate about changeovers or upgrades to procedures or equipment may result in confusion, injury and lost productivity. Before each change, companies must consider and document:
- Why the element is changing
- The technical considerations of the change
- How the change will impact employee safety or health
- The timeline required to implement the change
Taking these elements into consideration helps ensure all the fallout from proposed changes can be reckoned with safely and employees know how to react.
Process Safety Management Keeps Workplaces Safe
Some work environments require more risk considerations than others, but nobody needs to settle for an unsafe workplace. Employers are expected to provide all reasonable precautions for identified hazards — and employees are right to hold them to those standards.