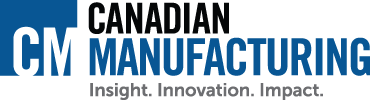
Thinking about reshoring? 3D scanning and digital twins can help
by Sadi Muktadir
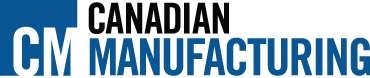
Currently, Prevu3D is involved in the food manufacturing space, helping manufacturers such as Agropur and Saputo reshore their operations from abroad.
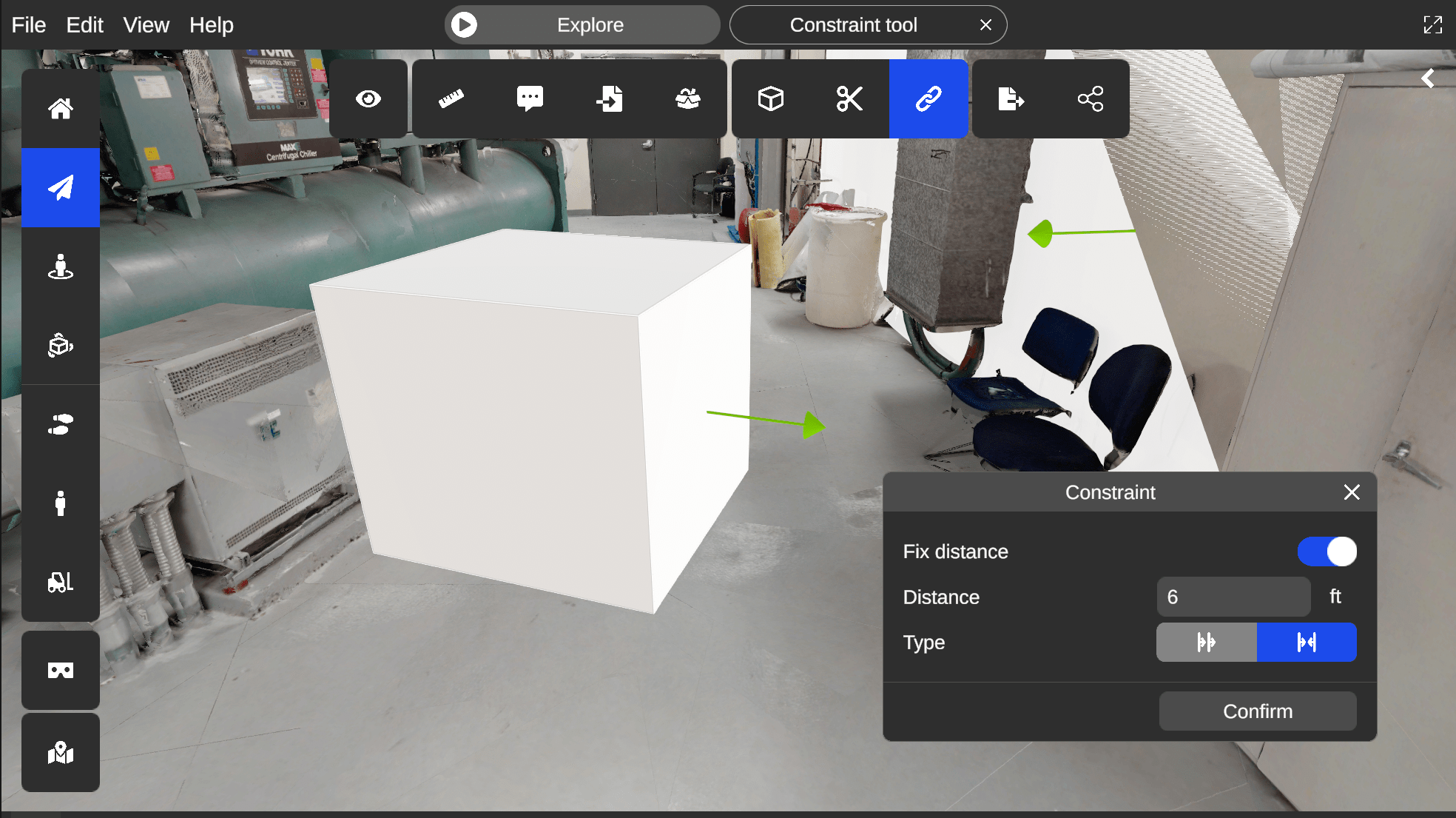
Thinking about reshoring? 3D scanning and digital twins can help
As the Omicron variant continues to ravage the Canadian economy, many manufacturers are looking to stay competitive and profitable with a lower headcount and ensuring their deliverables are made without any significant delays.
Advanced technologies have been deployed in many facilities by OEMs like Delta-Q Technologies to facilitate production and manufacturing on an automated line. One of the technologies being explored by many manufacturers is digital twins technology. A digital twin is a virtual representation that serves as the real-time digital counterpart of a physical object, helping to create products and equipment without defects or delays.
But what if the physical object is an entire factory?
That’s the question Nicolas Morency, Founder and CEO asked himself when he created Prevu3D.
Prevu3D is a company that is 3D scanning factories within a matter of days to try and help businesses become more efficient and optimal. Digital twins technologies are currently being used in the production process on parts and equipment, and Prevu3D is taking this one step closer to scanning an entire factory.
“Currently, equipment providers have 3D modelling in house, and we wanted to help facilities get access to this same equipment. 3D scanning is becoming very valuable and we think we’ve created a solution for people with no expertise in technology to be able to do virtual staging and see a project before it happens,” says Founder and CEO, Nicolas Morency.
Currently, Prevu3D is involved in the food manufacturing space, helping manufacturers such as Agropur and Saputo improve their operations and become more efficient through 3D scanning.
“We’ve moved 8 facilities already this way, cutting equipment and moving it around to fit into a new virtual space. In one instance we moved an entire factory from Australia to Canada,” adds Morency.
This is all to prevent further supply chain issues in the delayed deliveries of parts and equipment.
When asked how he came up with the idea for Prevu3D, Nicolas Morency spoke about his experiences as an engineer for manufacturers.
“I started in engineering, as a production line designer for manufacturers. I worked with a client once on a $140M project, where they flew us out every two weeks for a year and a half, but their design problem would have been solved in a matter of days if Prevu3D had been around at the time,” Nicolas explains.
Digital transformations are currently being undertaken across every major industry, and manufacturers acquiring new factories and production lines may be looking to take advantage of new spaces or squeezing more out of old ones.
“The food and beverage industry has been our main target for the most part, but we’re now speaking to some OEMs and we can see how we’d be able to help the oil and gas industry rethink their operations as well for improved benefits to the environment through reducing their emissions,” says Nicolas Morency.
Currently, 3D scanning an an entire facility involves hiring a 3D scanning company to model the facility by hand, taking months, and Prevu3D’s offering hopes to challenge that paradigm to help manufacturers evolve in a matter of days.
Prevu3D says they are seeing an uptick in business due to lockdowns and a renewed emphasis by manufacturers trying to create a more domestic supply chain.