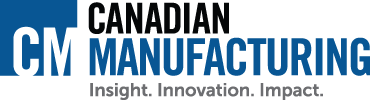
Three key factors impacting your labour costs
by Kronos Inc.
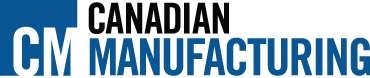
Small adjustments based on real-time data can boost profit margins
Sponsored article by Kronos Inc.
When it comes to workforce issues, perhaps no industry is under more pressure than manufacturing. The challenges include front-page topics such as massive outsourcing to low-cost countries, an aging workforce and skills shortages.
Having already automated many aspects of production and supply chain operations, manufacturers now recognize that the next frontier for high performance is the workforce.
“Labour is the next critical manufacturing element to optimize in today’s demand-driven world,” says Dave Caruso, principal at the manufacturing and supply-chain analyst firm, David Caruso & Associates.
“Savvy managers have realized that their workforce can be the engine that drives supply chains and manufacturing in the quest to move to the next level of performance.”
While most companies have automated core HR functions, many are just beginning to invest in strategic applications to rationalize the impact of the workforce on productivity and ultimately, profitability.
Unintended consequences
Overall labour effectiveness (OLE) provides a window into workforce productivity. OLE tools expose the impact of both direct and indirect labour, so manufacturers can take action to reduce costs and boost efficiency.
OLE gives companies the ability to analyze the cumulative effect of three workforce factors on productive output:
- Availability: the percentage of time the workforce spends making effective contributions;
- Performance: the amount of product delivered;
- Quality: the percentage of perfect or saleable product produced.
Improvements made to any one of these factors have an enormous influence on profitability. The historical challenge for many manufacturers has been to avoid the unintended consequences that can result when efforts to improve one area have a rebound effect.
“It didn’t take long to find that tweaking the numbers for labour availability, performance and quality by just one percentage point each made gross margin jump to 8.15 per cent and profit surge.”
For example, an initiative to improve quality might end up impairing output performance by slowing down the production line. OLE helps expose these inter-relationships and provide a real-time view of progress, so managers can keep all three measures in balance.
A recent example of OLE in action involved a chief operating officer (COO) at a large company preparing an annual budget. The COO started by using current standards to draft plans for projected production volumes.
This resulted in an expected gross margin of 6.25 per cent, with labour making up 10 per cent, overhead 66 per cent and materials 24 per cent.
It didn’t take long to find that tweaking the numbers for labour availability, performance and quality by just one percentage point each made gross margin jump to 8.15 per cent and profit surge.
The challenge, of course, was to find where the necessary improvements could be made. Using OLE tools, the COO found ways to boost output and quality by increasing the flexibility and cost-effectiveness of the workforce.
Overall, he identified a total of a three to five per cent improvement in labour costs. He also discovered the company’s outsourcing program was not delivering expected benefits.
Get more details by downloading the full report
The improvements at the company are just one example of the efficiency and increase in gross margins provided by an OLE approach.
Manufacturers have made great strides in optimizing materials usage by implementing powerful supply chain applications, but the labour side of the equation, which concerns a company’s most vital and controllable resource, has been largely neglected.
Companies have invested in basic HR functionality but are missing the productivity rewards that can result from optimizing labour availability, performance and quality of work.
OLE can give manufacturers the fuel they need to capture significant cost savings and improve their market competitiveness. It brings balance to the manufacturing equation of labour and materials; harnessing information about interactions between them and opening new windows of opportunity.
Kronos Inc. is a leading provider of workforce management solutions. To learn more visit Kronos for Manufacturing; or get in touch by clicking here
This article is part of the Productivity Success Centre, focused on boosting shop floor performance and cost efficiencies.