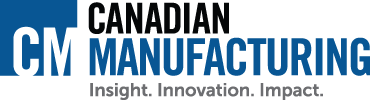
How banks and asset-based lenders differ in their thinking
by Ken Hurwitz
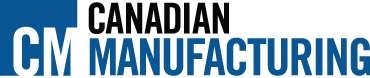
Understanding collateral, value and revenue requirements can speed your access to financing
—Sponsored article by Blue Chip Leasing
One of the most frequent questions I get from business owners as they begin planning an equipment purchase is related to the interest rate. Almost every customer I talk to, unless it’s a startup, already has a banking relationship and along with it, some form of operating line of credit.
It’s no secret that a bank is the lowest-cost provider of funds, for two reasons. First, these days the cost of funds for a deposit-taking institution such as a bank is less than one per cent, and maybe even less than 0.5 per cent. This means a bank can loan money at a few hundred basis points above the Canadian prime rate and still turn a very good profit.
Second, banks ensure their money is extremely secure. It’s not uncommon for a typical bank to have security worth three or more times the value of the money it is lending out.
Understanding the GSA
When setting up financing, I typically explain to the borrower the ins and outs of a general security agreement (GSA). A GSA is the document that provides a lender a security interest in a specified asset or property that is pledged as collateral. In the event that the borrower defaults, this pledged collateral is seized and sold.
This agreement, presented and signed when an account is opened, gives the bank the first chance at all current and future assets of the company. The key word here is future because most companies grow and accumulate assets over time. In manufacturing, this usually means machinery and other equipment.
For asset-based lenders, this becomes a problem when I close a deal by taking an existing piece of equipment as collateral, in lieu of a deposit, and I inform my client I need a waiver from their bank that supersedes the GSA.
The response I almost always get is this: “Why do you need a waiver if I paid cash for that equipment?” The waiver simply is a document that waives the bank’s interest in a particular piece of equipment. It’s usually a formality, but there have been instances in which the bank would not accommodate this request, or at least made it difficult.
Other recent deals that required waivers from a bank occurred when I wasn’t even requesting equipment as collateral. One customer desperately needed some new equipment and purchased a new machine they could get on their floor quickly and making money, and then arrange the financing later.
Because it is a well-established, financially strong business, they thought the order of events didn’t make any difference. They were shocked to find out my approval called for a waiver from their bank because the moment the equipment was paid for, it became an asset of the company and therefore part of the bank’s security.
What made it even more frustrating for my customer was the bank wouldn’t sign the waiver until it had both updated financial statements for the company and personal information from the owner. It was sorted out evenutally, but it did take time, effort, and added some aggravation. All to use money that was never the bank’s in the first place.
When it comes to equipment loans, banks will first look at the size of the transaction and whether it fits the equity box of the company. Specifically, banks will look at the company’s total net worth, the net earnings/profits not paid out as dividends to shareholders but kept in the company to be reinvested in its core business.
A bank will think the transaction fits if the money left in the company is twice the amount of the transaction size. For example, if you were looking to purchase a $100,000 machine, a typical banker would expect the retained earnings in the company to be about $200,000.
In the manufacturing industry, however, that type of evaluation becomes problematic because machinery is expensive and usually purchased when an opportunity for growth comes along. An example is when an order for parts is received, but the payment has not yet shown up on a financial statement.
Alternative to banks
A private leasing company is not a bank and gets its money from numerous places, but it is not a deposit-taking institution. Therefore, it has a higher cost of funds. However, leasing companies look at the $100,000 transaction and expect the company to have retained earnings of only $100,000. This automatically means a leasing company can approve more transactions than a bank could.
It’s important to keep in mind a new piece of machinery will depreciate the moment it’s installed in a manufacturing facility, no different than a car depreciates the moment it’s driven off the lot. This, combined with the fact that the leasing company does not require as much security, equates to a transaction that is slightly riskier than a typical bank transaction and so is not priced identically.
The difference between what a bank offers and what a prime credit leasing institution offers could be as little as 100 basis points, with the most important difference being that the transaction will likely get done in a timely manner with a leasing company.
In today’s competitive environment, it makes sense that every manufacturer wishes to ensure it is getting the best deal at the lowest possible cost. But, understanding the security that needs to be provided also should be evaluated as part of the transaction.
Manufacturers have many different alternatives for financing, and finding the right fit is just as important as sourcing the proper equipment for the job, and the same care should be taken to find the right financial institution.
Ken Hurwitz is senior account manager with Blue Chip Leasing Corporation, an equipment finance company in Toronto. Ken has years of experience in the machine tool industry and now works to help all types of manufacturers either source or tap into their own capital to optimize their operations. Contact Ken at (416) 614-5878 or at via email. Learn more at www.bluechipleasing.com
This column originally appeared in the January 2017 edition of Canadian Metalworking.
The article is part of the Financial Management Success Centre, showcasing strategies to access working capital, reduce costs, and leverage the value of shop floor equipment.