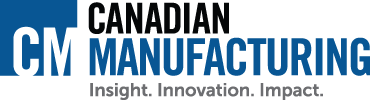
IFS announces acquisition of Cdn. worker technology company Poka
by CM Staff
Poka enables factory and field workers to be more efficient across all aspects of their jobs from training and development to troubleshooting.
LONDON — IFS announces that it has signed a definitive agreement to purchase Poka, Inc., a Quebec-based provider of a connected worker platform. Poka enables factory and field workers to be more efficient across all aspects of their jobs from training and development to troubleshooting. This capability enables businesses to measure productivity across machinery and operators globally and tries to provide a clear insight into profitability. Poka also provides actionable insights for companies to stay compliant and provide safer working conditions as part of their ESG goals.
Over the past decades companies have invested trillions of dollars enabling back office workers to do their jobs. With the massive focus on efficiency, industry 4.0 and the merging of the physical and digital worlds to drive automation, companies are now looking to enable factory and field workers to work smarter, safer and more efficiently.
The acquisition puts IFS at the nexus of this trend as it now combines its ERP / FSM / EAM technology with Poka and extends its value all the way to the actual user empowering them at every step.
Founded in 2014 by Alexandre Leclerc and Antoine Bisson – the company has customers in 55 countries which include brands such as Nestlé, Tetra Pak, Mars, Bosch, RioTinto, Coty, Alcoa, Hitachi Energy, Mahle, and more. For companies such as these, recent global events have created a heightened degree of complexity, and uncertainty in labor availability as well as impacted supply chains and raw material sourcing. To address these business challenges, organizations are doubling down on their efforts to achieve faster digital transformation. At the heart of this renewed focus is the need to empower their own employees making the Connected Worker a key focus.
Connected Worker technologies go beyond delivering a software application to help workers do their jobs better. When frontline workers are digitally connected, companies are better able to gather and share critical operational data real-time, leading to optimized work systems where insights are contextualized and responsive.
IFS CEO, Darren Roos, commented “The concept of a connected worker is synonymous with the augmented worker because of the direct impact on improving productivity and operational efficiency. With a potential manufacturing skills gap in the U.S. alone which could result in 2.1 million unfilled jobs by 2030*, closing this gap, it is as much a technology need as it is a change management and worker empowerment need. Improving access to information and knowledge means workers can become part of an integrated continuous improvement cycle.” Roos added: The concept of connecting every single worker was historically overlooked as part of digital transformation journeys yet, giving workers the ability to get information whenever and wherever they are in the factory not only improves their experience, it is fundamental to building manufacturing agility something we understand very well at IFS.”