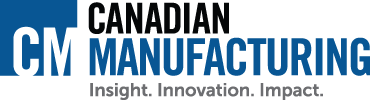
Ultra-precision micromachining meets optical metrology
Optical metrology solutions collect millions of data points for improved error correction in micro-tolerance applications.
Micromachining has gained a lot of attention over the last several years, representing an area of growth, particularly for North American manufacturers.
While some more simplistic applications have been sent overseas, the micromanufacturing industry faces a greater level of complexity that many companies are unwilling to outsource.
As micro-components continue to shrink in size and grow in complexity, manufacturers must determine the necessary machine platforms and measurement systems to produce and verify increasing demands for accuracy and surface finish.
Ultra-precision machining centres and metrology systems go hand-in-hand. With advancements made in either field, new opportunities for component miniaturization arise. Mould manufacturers should be encouraged to marry these technologies in their own shops to improve quality, verification and inspection.
The foundation for accurate, repeatable and predictable processing of micro-tolerance tools and moulds lies in the construction and resolution of a machining centre.
Many machines on the market today try to reduce vibration through software rather than solving vibration at the source. The most consistent way to eliminate vibration is to design rigidity into the machine with sound construction fundamentals. With a heavy-duty construction and appropriate slide way design, machine vibration can be eliminated before it occurs.
The most critical features of an ultra-precision micromachining centre are its dynamic thermal stability, and mechanical and control resolution — the scale for which a machine’s accuracy and predictability can be measured.
The higher the thermal stability, combined with the resolution level of a machine’s motion control system, the more accurate and repeatable the machining process becomes.
For this reason, premium micromachining centres are now being designed with 0.01 micrometre (μm) or 10 nanometre (nm) resolution— approximately 10 times the resolution of standard machining centres. This level of resolution allows manufacturers a higher degree of programmable accuracy and predictability in the adjustments of the machining process.
There are a variety of metrology systems on the market today however, micromanufacturers must pay close attention to the specifications, including measurement size and volume.
To ensure high accuracy, an appropriate metrology solution needs to provide repeatability and reproducibility of 10 per cent or less than the desired tolerance.
Error correction can be increased by collecting more surface data points. The use of touch probes within micro-tolerance applications is not always effective and is limited by the physical size of the contact stylus.
More modern optical metrology solutions can avoid these issues entirely, through the use of white light scanning technology. Where other technologies can record 100 to 1,000 data points, optical metrology systems collect millions of data points in a relatively short measurement cycle.
Each point can be displayed as a full three-dimensional surface map that reveals elaborate details on the surface roughness, form and flatness. This surface map can then be overlaid against the original design model to closely evaluate errors and make informed adjustments to the machining process, allowing for improved accuracy and quality.
The combined use of these high-performance machining centres and precision metrology systems now make it possible to produce features as small as 10 μm. However, certain conditions should be considered to ensure this level of precision.
Choosing the appropriate machine process, whether it be milling, EDM or any other technique, is a decision that must be made based on the features and specifications of the application at hand.
John Bradford is the micromachining team leader at Makino Inc., in Auburn Hills, Mich.
This article was provided courtesy of Manufacturing Engineering Media, a division of the Society of Manufacturing Engineers.