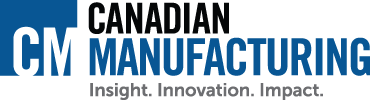
Carbon captured filament for 3D printing no longer a dream of the past
by Sadi Muktadir
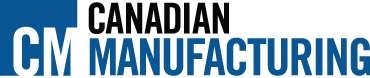
Oco captures flu gases from power plants and purify it using their rotating ball mill until powder additives come out.

Photo: ©Sutthiphong/Adobe Stock
The net-zero push is in full swing across all industries, not just electric vehicles.
3D printing is a burgeoning industry seeing Canadian players adopt sustainability practices across all aspects of their supply chain, with many additive manufacturers using recycled materials to minimize the plastic waste generated through the printing process.
One company is taking this a step further. Oco, a subsidiary of Carbon Upcycling, recently announced their capabilities in capturing carbon into a filament for 3D printing, and Peter Zhou, the Product Development Lead, says they are just getting started.
“We’re very excited to be ramping up production. We’re working on new resins and new materials to bring to market and we’re scaling up, capturing flu gas and solid sorbent into captured CO2 for new products,” says Peter Zhou.
Oco captures flu gases from power plants and purify it using their rotating ball mill until powder additives come out. Solid sorbent is milled down along with the CO2 to create a material that can be manufactured into a variety of things, such as soap, fertilizers and glass.
Oco’s Product Development Lead was asked about some of metrics around the captured carbon material, and how fast it can be printed or used in manufacturing.
“Currently, 20 metric tons of captured carbon content per batch of clean CO2 results in 200 metric tons of printable filament. And this takes about 3 months to convert into kilogram spools for consumers. We also recognize that the cost of utilization right now is high, ranging from $500-$700 per metric ton, when regular 3D printed material is around $200 per metric ton.”
When Peter was asked about what made their technology advantageous for manufacturers, he was clear.
“The urgency for 2050 starts today,” he says, in reference to Canada’s commitment to be net zero in emissions by then. “The merits to look at something small like CO2 capture make sense right now. We hope the manufacturing community knows it can be used and adopted at a wide scale.”
Other players in the 3D printing and additive manufacturing space were intrigued by the idea as well.
“Capturing carbon into filament is something I have not heard about yet but it sounds super cool,” says Mitch Debora, Co-Founder and the CEO at Mosaic Manufacturing, an additive manufacturer.
“Many companies have swapped from a plastic spool to a 100% recycled cardboard spool so that you minimize plastic waste generated through the printing process and effectively getting rid of a single use plastic,” he added.
Additive manufacturers are exploring ways to make the industry more sustainable through new filaments and when asked about the current roadblocks to wider adoption, Peter Zhou said that ‘education’ was one such factor, and the industry should know that their filaments are plug-and-play, and can be used in open-source printers, including on Prusa, Enders, Neptune, and any other manufacturers.
Oco says they are continuing work on other aspects of the additive manufacturing supply chain, hoping to localize recycling solutions as well, including dumping failed prints and bad parts into new filaments that can be reused.
As they build their client lists, companies like Oco will be interesting to follow. Which manufacturers sign on as early adopters of carbon-captured filament will reveal where the industry itself is headed.