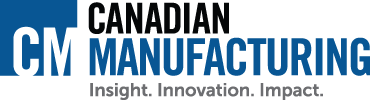
Manufacturing in a Connected World: The Principles of Industry 4.0
by Steve Bassaw, Product Manager, Syspro Canada
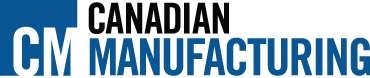
Four design principles underpin the journey to achieving the full potential of Industry 4.0
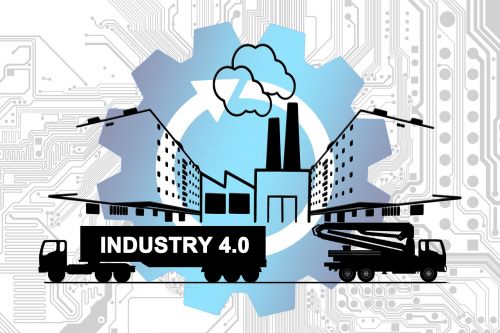
PHOTO: Needpix.com
—Sponsored article by Syspro Canada
In a recent survey, 70 per cent of manufacturers said they expect new competitors from other industries to leverage Industry 4.0 to enter their markets, while 90 per cent believe that Industry 4.0 will help them compete. Clearly, the competitive landscape is changing, and you need to keep pace in order to survive.
“Industry 4.0 is a subset of digital transformation as it applies specifically to manufacturing and distribution companies,” explains Jonathan Gross, Managing Director of Pemeco Consulting, a company that specializes in ERP consulting services.
It’s about making manufacturing more efficient and empowering personnel to make decisions. You need to be able to deliver “last mile” configurations and customizations to your customers, and that’s where your systems can really improve your ability to perform this. Timely and accurate data is necessary for personnel to make effective decisions and machines to take autonomous action.
Let’s look at the four design principles of Industry 4.0 that are crucial for businesses to embrace in order to realize the full potential of Industry 4.0 technology.
Interconnection
Your architecture must be set up in a way to connect your systems with your people, meaning your machines, devices, and people are able to communicate with one another in real time, thereby ensuring everyone is on the same page.
Information Transparency
The data collected through interconnection must be transparent — both ways (once again, from the physical to the cyber world, and then from the cyber to the physical world) in an efficient and timely manner (in some cases, in real time, but at the very least, when needed). This will thereby allow people to make any decisions that fall outside of the parameters that the systems are programmed to handle.
Technical Assistance
There are two parts to this principle. Firstly, we want to ensure machines do the things they are really good at and can deliver the most value, namely providing technical assistance (in an Industry 4.0 perspective), by performing low-value and repetitive machine-oriented tasks, which will subsequently free up your human resources to focus on higher value tasks. The flip side here is that the systems will provide to your staff the data and analysis necessary to make timelier and more effective operational or strategic decisions. Ultimately, the cognitive learning and artificial intelligence underlying these systems will discover new data sets, allowing us to view the information in new and more useful ways (for instance, on the operations side, ways to save costs; and on the strategic side, uncovering new cost analysis or revenue opportunities).
Decentralized Decisions
Our enterprise software systems and machines must be empowered to take autonomous action as that’s the key to driving efficiency. Naturally, this will come with parameters – “we’re not going to let the robots take over the world,” Gross says. For instance, data is being analyzed by your systems to determine when the ideal time is to schedule equipment maintenance and/or order replacement parts. This will take into account both wear and tear and peak demand times to ensure the maintenance is the least disruptive possible. In this instance, optimization is gained by removing the possibility of human error that could lead to equipment failure and the resulting costly downtime.
Now that you understand the basic principles behind Industry 4.0, it’s time to get started. Download our recent webinar Manufacturing in a Connected World 101: Getting Started to learn more about how companies like yours are implementing their digital strategies along with best-practices methodology to develop your strategy and execution plan.
Steve Bassaw, Product Manager, Syspro Canada, is a supply chain professional of 20+ years including Planning, Scheduling, and Purchasing, and has the APICS CSCP designation (Certified Supply Chain Professional). Steve has been with SYSPRO for 19 years in diverse roles such as Support, Consulting, Product Management, and Solution Architect. Before joining SYSPRO, Steve was a SYSPRO software super-user at a manufacturing company where he gained hands-on experience using ERP to improve Operations and Supply Chain. Steve is also Chair of the Advisory Committee for BCIT’s Business/IT program, contributing his knowledge on how information technology is used to support real-world business requirements.