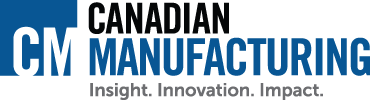
How accurate is your payroll?
by Kronos, Inc.
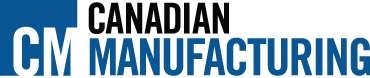
Use Six Sigma to deliver the perfect paycheck—one that is accurate, ready on time and produced for a predictable cost.
Sponsored article by Kronos, Inc.
Delivering the perfect paycheck is not as simple as it seems. Once you factor in variables like overtime, leave, shift differentials, vacation, union agreements and regulatory considerations, delivering the perfect paycheck just got a lot harder.
The good news is that the perfect paycheck—one that is accurate, ready on time and produced for a predictable cost—is still an achievable goal.
Seeking the perfect paycheck
Six Sigma examines a number of metrics that make up how an order is manufactured and shipped, giving manufacturers a benchmark to measure production performance. These techniques can be applied to the production of a paycheck. Think about the timekeeping and payroll process as a production line and each paycheck as an order that must be delivered to a customer. The goal is to measure delivery, quality and production costs associated with the paycheck.
Finding defects
The first step is to reduce defects in the payroll process. Off-cycle checks, overpayments and underpayments, and overriding the documented payroll approval process are all examples of defects that occur in payroll processing.
Understanding how close your process is to achieving the perfect paycheck begins by evaluating your current quality level. In a recent study, the American Payroll
Association estimated the payroll error rate at two per cent (20,000 defects per million).
While this may seem like a relatively low rate, correcting and paying for 20,000 errors could lead to a significant payroll expense with no customer value. And Six Sigma allows only 3.4 defects per million.
Once you have identified errors, examine their causes. You can start by imagining what your payroll error rate would be if every employee earned the same wage and worked exactly 40 hours each week.
You’d probably be looking at an error rate approaching zero, and you would have a Six Sigma process. But in reality the hours and wages worked and earned by your employees are affected by daily, spur-of-the-moment issues, regulatory requirements, and the variability that occurs within the payroll production process.
How Six Sigma Can Make a Difference
Six Sigma provides tools and processes to help organizations identify which variability is causing the greatest number of errors, along with controls to help manage that variability. It’s important to recognize that Six Sigma is not a cure-all. It requires understanding business processes and applying creativity to resolve problems.
Six Sigma follows a five-phase project methodology:
Define: This phase defines the project objective, such as achieving a desired sigma value or reducing the cost of per-paycheck processing from $3 to $2. It’s an important step that drives the direction of all other phases. For example, if your objective is to reduce cost, when you reach the measurement phase, you would define where excess costs are added to the process rather than measure errors.
Measure: Choose characteristics that are critical to delivering the perfect paycheck, based on the project definition and understanding the current capabilities of the process. This step requires participants to be familiar with the payroll process and will require some data and facts about the process. One method to organize this information is a Design Failure Mode and Effects Analysis, a visual representation that helps participants understand what causes the failure to deliver the perfect paycheck, the frequency with which failure can occur, and the severity of the impact of the failure.
Analyze: With the data in hand, it’s time to look for cause and effect and identify the root causes of payroll errors. A common tool for this analysis is the Ishikawa diagram, sometimes called the fishbone diagram. The Ishikawa diagram starts with six possible causes: Method, Man, Machine, Material, Measurement, and Environment.
Improve: Once root causes have been identified, you may find yourself wondering how you’ll marshal the resources to fix them all at once. Performing a Pareto analysis can help. The Pareto principle—often called the 80/20 rule—states that 20 per cent of the issues cause 80 per cent of the problems. Figuring out the 20 per cent causing the biggest problems is a good way to prioritize your efforts.
Control. After you determine which process improvements to implement and the changes have been made, it’s time to move on to controlling the process. Your new payroll process should have less natural variation and benefit from higher quality and lower costs. But assignable variation can still occur because not every root cause will be eliminated, and old habits have a way of creeping back into the process. By measuring the output of your payroll process, you can continuously check quality and address any variability.
Because the tasks required to deliver a paycheck involve many departments, a formalized improvement process such as Six Sigma can be a good foundation for achieving success.
Kronos Inc. is a leading provider of workforce management solutions. To learn more visit Kronos for Manufacturing; or get in touch by clicking here